AZIWELL, International Directional Services de Mexico, and Layne de Mexico for Minera Media Luna - a subsidiary of Torex Gold.
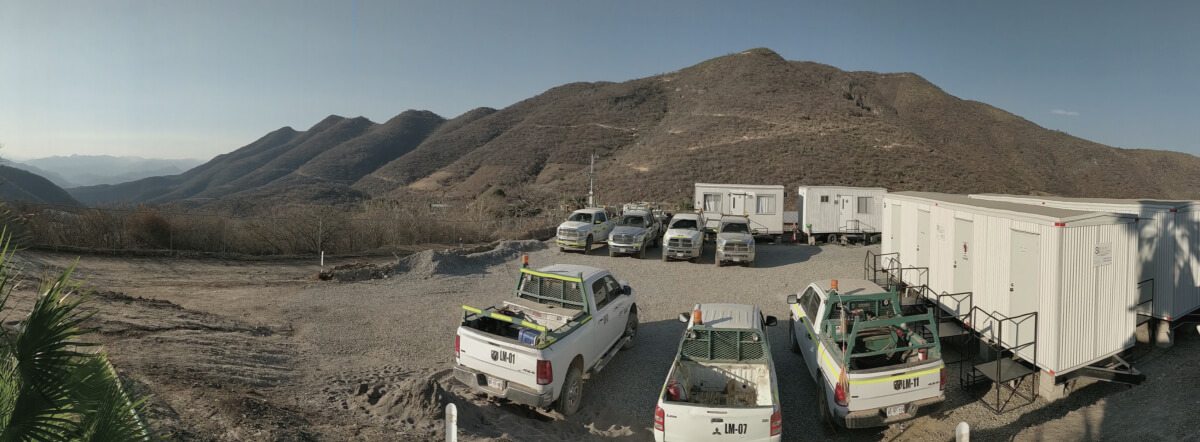
by Nils Ivar Iversen, Chief Executive Officer AZIWELL, Daniel Popescu, Office Manager AZIWELL, and David DuCote, Operations Manager IDS de Mexico.
About 260 km (162 mi) southwest of Mexico City, on the southern bank of the Balsas River in Guerrero state, Torex Gold planned an intense infill drilling program at its Media Luna project.
Due to the site's topography, environmental regulations, lack of hydrological resources, and highly variable geologic conditions, a conventional drilling program would have been almost impossible to execute with the desired accuracy and within budget.
Phase I of the program began in October 2018 and consisted of 117 targets divided into 16 blocks, reached from only nine drilling sites. Each collar comprised of one block with nine targets, designed on a 30- by 30-meter (98.4 x 98.4 ft) grid spacing, to upgrade the deposit to ‘measured’ status.
Setting
Media Luna is a skarn deposit located in the Morelos district, itself a part of the Guerrero Gold Belt. Its geological setting is dominated by limestone, siltstone, and other sedimentary formations cut by several intrusive bodies. The resulting contact metamorphism leads to the formation of skarns, rich in gold, copper, and silver.
The varying, thick sedimentary layers and the variety of intrusions create a unique set of circumstances that come with their own unique set of challenges for anyone attempting to drill through them.
Problem(s)
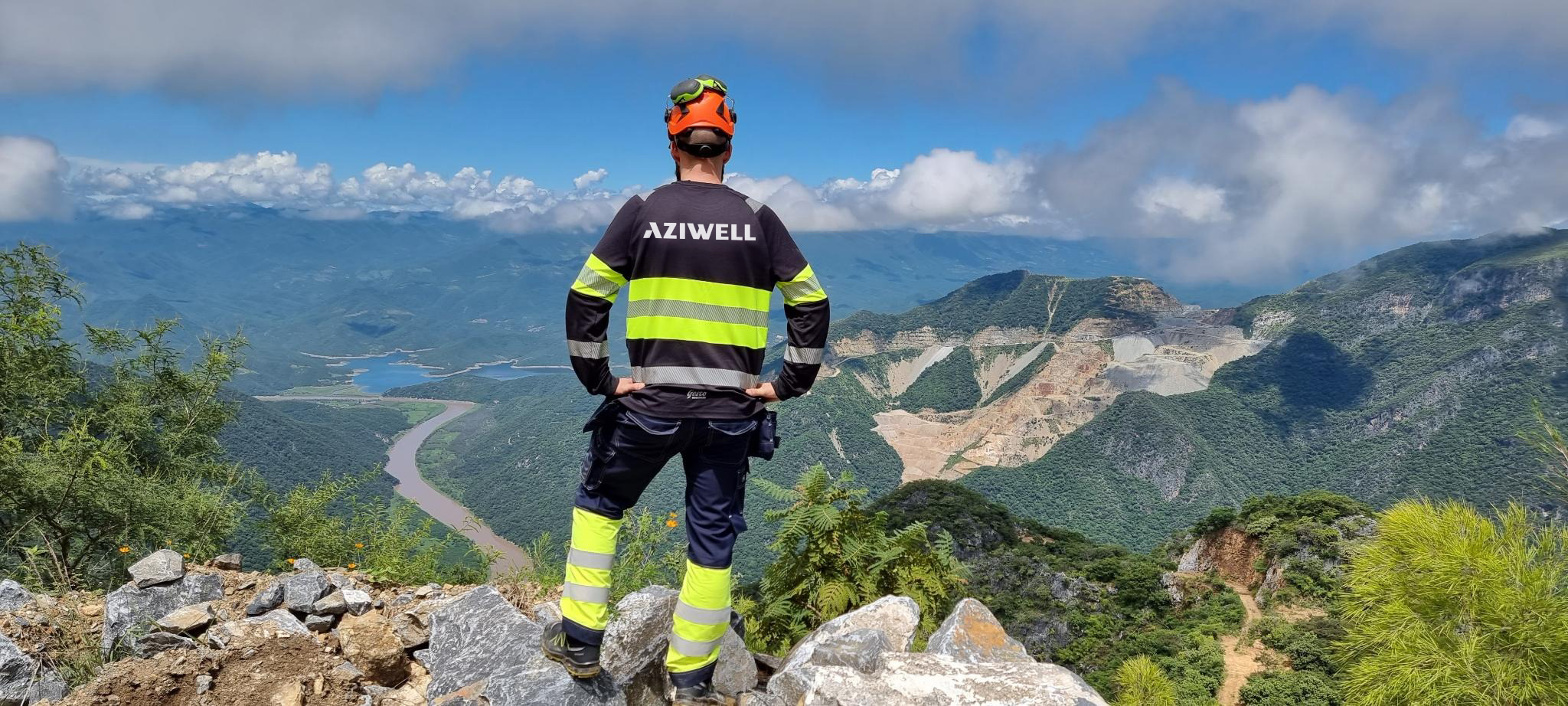
One of the main issues encountered was the lack of hydrological resources. Considering drilling is dependent on having a reliable water supply, any planned program had to contend with the limitations of having to bring in water to the project by tanker trucks.
Throughout its geological setup and structural deformation, the limestone in the area has been heavily affected by karst processes. That presented another problem for the drilling program, where the underground caverns created could lead to a total loss of water in a drilling well, further exacerbating the previously mentioned issue.
Extreme magnetic anomalies were also present due to the iron-rich exoskarn. This prevented the reliable use of magnetic measurment instrument.
The solution
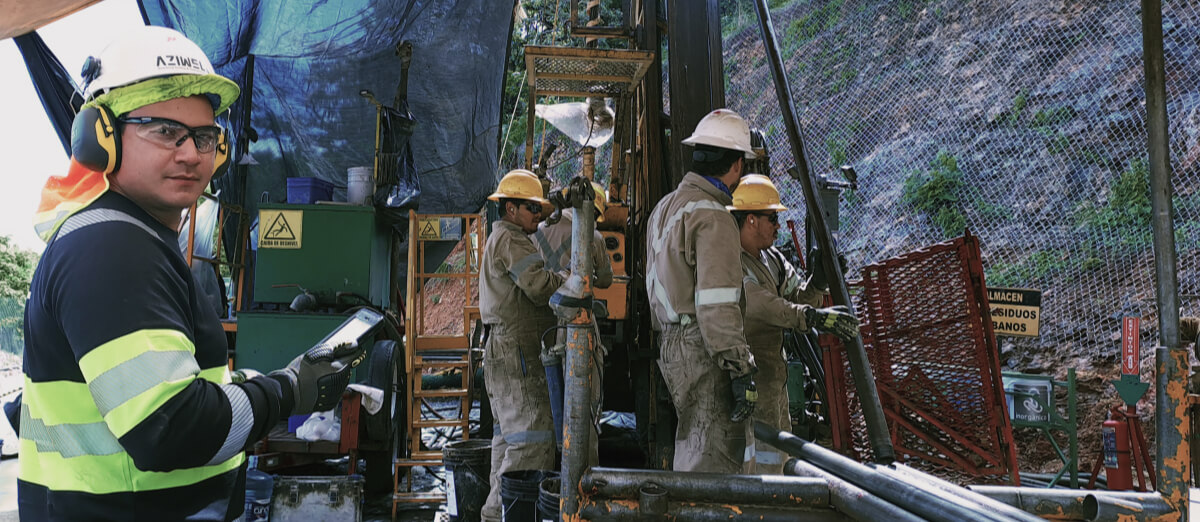
To save costs and reduce water consumption, the total number of meters drilled to intercept each target had to be cut drastically.
The only way to reduce meters while still reaching the same number of targets is to use directional drilling. In the simplest terms, it consists of producing an intentional and controlled deviation of a borehole to pre-determined target coordinates (Northing/Easting/Elevation). And of course, multiple deviations can be made from a single pilot hole.
The only way to reduce water consumption is to use a borehole steering tool. Borehole steering itself can be done with ‘full-face’ tools, or with ‘). An advantage of the DCB is that it uses far less water compared to a full-face tool such as a mud-motor, since it has no turbine that requires a higher flow volume. Furthermore, its ability to extract core increases the production rate compared to the alternative.
As such, the AziDrill® NB DCB was chosen for the task. The AziDrill® cuts an N-sized hole and collects a B-sized core sample. In addition, the DLS (Dogleg Severity – a measure of the drill hole curvature), tool face (orientation), and borehole trajectory can be continuously monitored to make timely adjustments and maintain the planned course of the curve. In particular, DLS needs to be kept within ‘safe’ parameters, as to not create an unacceptable amount of torque in the drill string which can then lead to a host of additional problems.
Planning
In every case, the mother hole was aligned to the center target and drilled to total depth before planning the daughter holes. This allowed the exploration team to select KOP’s (Kick-off Points) in favorable zones, and eliminate the risk of setting wedges, or beginning directional operations in unfavorable ground conditions. Each mother hole became the origin of eight additional daughter holes.
Due to the relatively shallow depth of the deposit of approximately 450-600 m (1476-1968 ft), every directional curve was designed to be completed with a length of about 40 m (131 ft) (on average). Although the AziDrill® collects a core sample during operation, extracting full-sized N core samples from the deposit was imperative, so the AziDrill® would have to be switched for the standard core barrel after the curve was completed.
Planning
Directional hole stages
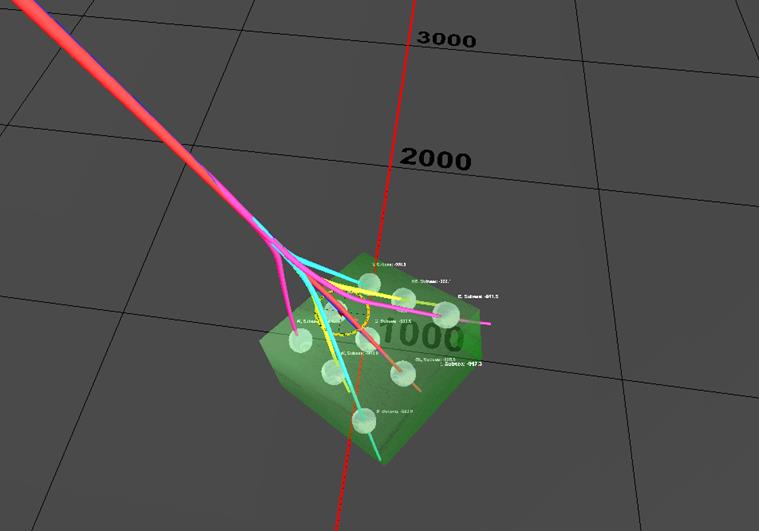
Mother holes began with collar alignment set to the central target based on the known natural deviation from the area. This was the only hole in the block where drill rig alignment was required. In all cases, holes were started with P-sized diameter for the collar and were advanced up to a depth of approximately 170-210 m (558-689 ft), where lithological and structural conditions demanded a reduction to H-size. The holes in which borehole steering was used were further reduced from H-size to N-size using standard core barrels and casing wedges.
Upon completion of the directional curve, the AziDrill® was pulled out of the borehole and standard drilling continued until the target was drilled and the borehole surpassed the limit of the skarn deposit.
In addition to drilling the curved sections, AziDrill® was also utilized to control standard drilling sections, such as mother hole corrections, where ground formations caused substantial natural deviation.
Wedges
After analyzing the core samples of each Mother hole, lithological and deviation information was considered to confirm the KOP, or if necessary, to propose an alternative KOP depth with better borehole conditions. Afterwards, anchors were installed as the base for the wedges.
For this project, two types of wedges were used: permanent by-pass and P/H-size Casing, the latter being recoverable and reusable. Once on the hole bottom, the wedge is oriented with a tool face directed at the target. Subsequently, the wedge ramp was drilled off using a bull nose bitball bit, reducing the diameter of from H-size to N-size. This methodology yielded three daughter holes per KOP (approximately 120 degrees of separation between each tool face orientation).
In general, it is not necessary to extract the casing wedge upon completion of a daughter hole. Simply lift the drill string, rotate to desired orientation, and set it down upon the anchor again. This is a very effective method for eliminating the amount of time involved in setting permanent wedges.
Gyroscopic Measurements
To monitor the trajectory of each borehole and create an accurate model of the deposit, it is necessary to collect frequent deviation measurements as the drilling advances.
Due to substantial magnetic interference in the area, all deviation surveys were collected via North-seeking gyroscope. These instruments are unaffected by magnetism. Additionally, these gyroscopes were utilized to validate the survey data collected by the AziDrill® during the curves.