Advantages of borehole steering technology using GEORAPTOR®:
- Steer any borehole fast and easy with precise targeting and multi-branch boreholes.
- Does not require third party field engineers.
- Reduce environmental footprint through reduced drill pads, operational time and CO2 emissions.
- Eliminate the use of steel wedging and mud motors.
- No depth limitations.
- Operate with ease. No special pumps, rods or rigs needed.
The GEORAPTOR® directional barrel provides an efficient way to steer your boreholes straight to target. Hit your targets at first try, make multiple branches from one borehole, reach of otherwise impossible areas, or make horizontal holes with a pre-determined path right on the target. All above can easily be achieved without the requirement of third party field engineers on site.
Show your interest today and you will be prioritized once the tool becomes commercially available!
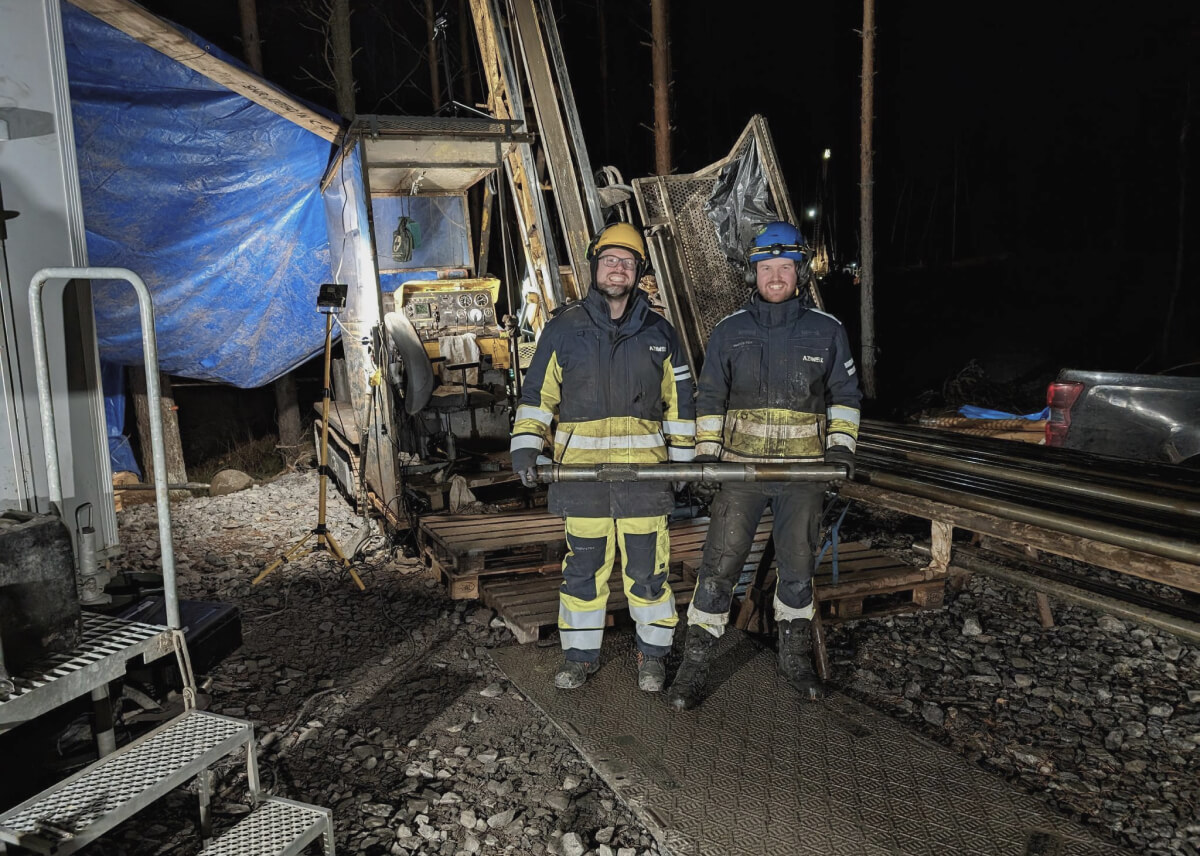
Save time & money
Time and cost savings on exploration drill sites using GEORAPTOR® are typically 20 - 50% compared to only utilizing standard conventional drilling with or without traditional steering methods such as wedging og mud motors.
With directional drilling, you can achieve the following:
- Reduced operation time
- Reduced number of meters drilled
- Reduced total cost of project
- Reduce the number of drill pads required to reach your targets
- Reduce water consumption and CO2 emissions
Easy to use
The GEORAPTOR® is fully compatible with standard N-size drill rods. No hole reaming before or after, no special rods or water pumps needed. The equipment is only 1m long, making it easy to handle. Just replace your standard core barrel with the GEORAPTOR® and you are ready to steer the borehole.
The GEORAPTOR® collects data such as direction and inclination of the borehole through sensors sitting in the head assembly. The data is easily checked whenever the operator wants to by retrieving the head assembly to surface. Due to the short length of the GEORAPTOR®, azimuth readings with a gyro can be made just 1m above the bottom of the borehole. The hole path and degree of deviation is monitored and changed when needed to accommodate your drill plan.
GEORAPTOR® equipment package
The GEORAPTOR® equipment package is available for trial Q1 2025 and contains:
- One complete GEORAPTOR®
- One complete spare GEORAPTOR®
- NAVIGATOR™ borehole planning and optimizing software
- Suitable accessories of spare parts and diamond products
Technical data
Physical spesifications
Operational spesifications
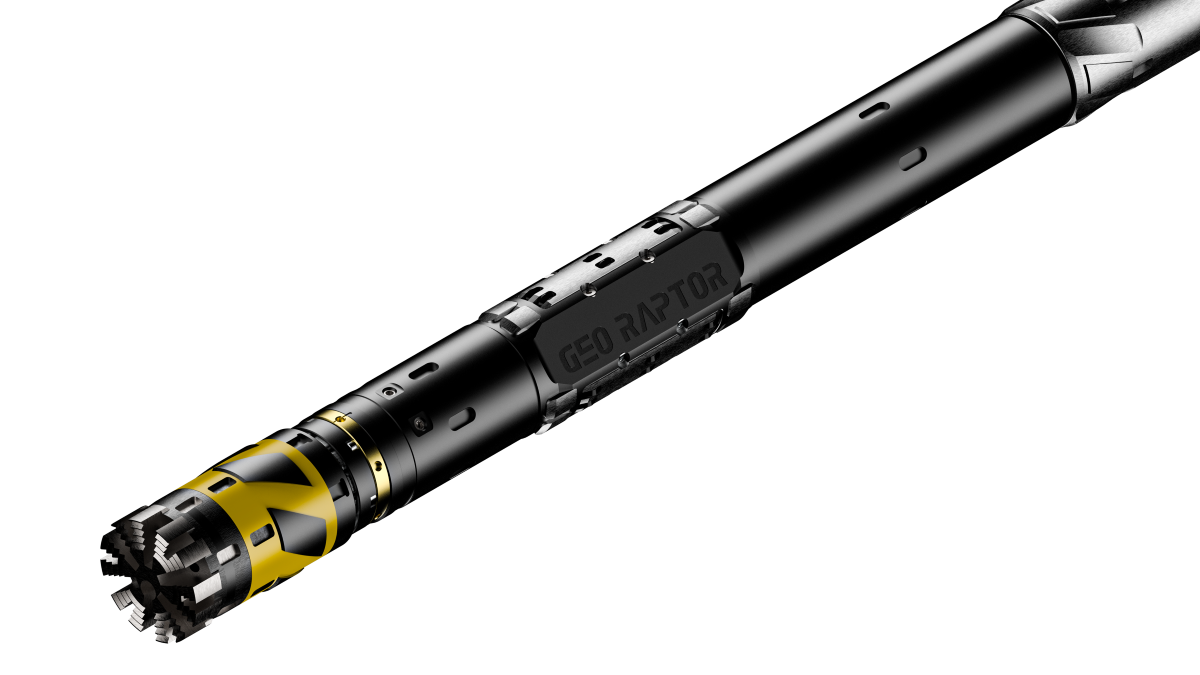